How Alabama’s Growing Industries Benefit from Advanced CNC Plasma Cutters
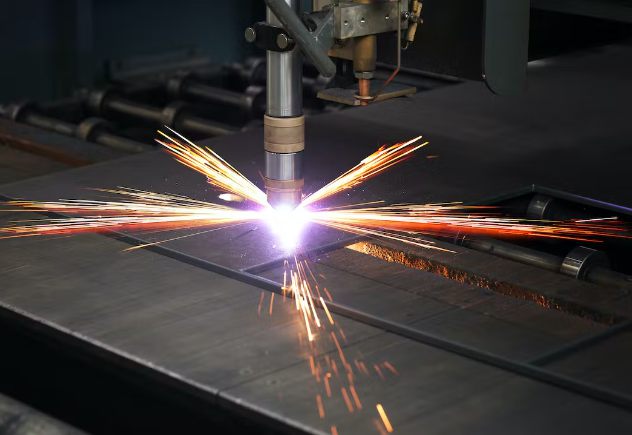
Across Alabama, modern manufacturing is making big moves—and not with guesswork. Behind the scenes, precision machines are reshaping how metal gets cut, shaped, and assembled. From metal shops in small towns to full-scale production floors, CNC plasma technology is helping businesses do more with less waste and more speed.
Rapid Throughput Elevates Output for Alabama’s Metal Fabrication Sector
Speed isn’t just a luxury in metal fabrication—it’s a necessity. Today’s Alabama workshops are expected to deliver complex parts fast without compromising quality. That’s where the advanced cnc plasma cutter in Alabama steps up. With faster cutting speeds and reduced manual handling, metal shops now push out finished components in record time. This high-throughput advantage is giving local businesses a serious edge in competitive contracts and delivery schedules.
A modern Alabama plasma cutter can slice through thick steel or aluminum sheets in seconds—what used to take hours with traditional methods. It’s not just about cutting faster; it’s about staying ahead. As industries grow across the state, from aerospace to construction, the demand for dependable output keeps climbing. Shops that embrace plasma automation are already reaping the rewards with bigger jobs and better timelines.
Micron-Level Accuracy Eliminates Expensive Metalwork Revisions
Metalwork mistakes cost more than just materials—they eat into labor time and project schedules. The latest Alabama CNC plasma cutter systems now bring pinpoint accuracy to the table, down to the micron level. That kind of precision means parts fit right the first time, whether it’s a custom bracket or a high-stress engine component.
For an Alabama robotics engineering company, having dependable cutting accuracy changes the entire workflow. Instead of backtracking to fix warped edges or incorrect cuts, teams can move forward with assembly. That ripple effect—saving time, materials, and headaches—is why more Alabama manufacturers are turning to plasma innovation as a cornerstone of their production line.
Intricate Component Fabrication Simplified Through CNC Plasma Innovation
Detailed parts once required multiple machines and skilled operators. Now, an advanced plasma cutter in Alabama can handle it in one pass. Tight curves, sharp angles, and internal cuts that once required tedious hand-finishing are now streamlined with smart software and CNC control.
- Intricate HVAC vents? Done.
- Decorative metal fencing? No problem.
- Complex enclosures for electronics? Easy.
Even small-to-mid-sized Alabama shops are discovering the creative freedom these systems offer. With CAD-driven precision and real-time monitoring, even the most intricate requests become everyday tasks. This shift is helping smaller teams compete with larger manufacturers by giving them access to the same high-tech capabilities.
Reduced Machinery Idle-Time Enhances Profit Margins for Alabama Industries
Idle machines don’t just sit—they cost money. Whether it’s waiting on setup, reprogramming, or repairs, downtime adds up fast in busy Alabama shops. But the new generation of Alabama CNC plasma cutters solves that with smarter scheduling, faster setup times, and fewer breakdowns.
A growing robotics engineering company in Alabama knows the value of consistent machine availability. Fewer breakdowns and smarter diagnostics allow production to stay on track longer. When machines cut more and sit less, businesses boost margins without adding hours or staff. Across industries like automotive, construction, and aerospace, uptime is becoming just as important as speed.
Optimized Material Usage Drives Notable Cost Efficiencies
Wasted metal isn’t just waste—it’s lost money. With precision nesting software and refined cut paths, Alabama plasma cutter systems are turning once-scrapped material into usable inventory. These systems tightly arrange cuts to maximize each sheet of metal, reducing leftover trim and throwaway sections.
That efficiency adds up quickly, especially for companies dealing with fluctuating steel and aluminum prices. A smart cnc plasma cutter in Alabama not only boosts output but helps control costs long term. For manufacturers that juggle large volume runs and custom orders, that smarter material use is changing the game from quote to delivery.
Versatility Across Metal Alloys Unlocks New Industrial Opportunities
Different projects require different metals—and a quality Alabama CNC plasma cutter is ready for all of them. Whether the job calls for mild steel, stainless, copper, or exotic alloys, these machines adjust quickly. That kind of flexibility opens doors for new partnerships, markets, and contract opportunities.
An Alabama robotics engineering company focused on custom manufacturing can now respond to a wider variety of client needs without switching tools or delaying production. One day it might be agricultural parts, the next it’s aerospace panels. Having that versatility means fewer limitations—and more room to grow with evolving industry demands.
Streamlined Operational Expenditures Amplify Profitability for Alabama Manufacturers
Cutting costs doesn’t always mean cutting corners. By upgrading to smarter systems, Alabama manufacturers are lowering overhead in quiet but powerful ways. Energy-efficient machines, minimal operator supervision, and simplified training all help reduce ongoing costs.
When a robotics engineering company in Alabama installs advanced plasma solutions, they’re not just improving how they cut—they’re reshaping how the entire operation runs. With fewer inputs and stronger outputs, profitability becomes more sustainable. And as more Alabama industries recognize this, the shift to smart plasma automation is becoming less of an upgrade—and more of a standard.